Client challenge
While planning for an upcoming turnaround, the customer realised that a significant number of inspections required both Guided Wave Ultrasonic Testing (GWUT) and Radiography Testing (RT). The company had low confidence that the existing plan optimised the resources needed and it was unsure if other inspections were being overlooked.
Being constrained by internal resource availability and lacking significant in-depth corrosion experience, the company requested the assistance of Vysus Group to perform an independent, third-party review of the current inspection plan and of the Condition Monitoring Locations (CML) during the turnaround planning period and develop a comprehensive and optimised execution plan.
How we helped
We deployed a team consisting of Inspection Planning Engineers and Corrosion Engineers to review and evaluate each damage mechanism that a circuit is susceptible to. We then developed a strategy document that guided the user on how to identify susceptible locations and determine the coverage required. The document was then used to red line the inspection drawings.
The red lines included marking locations that were no longer required to be inspected, a better inspection technology to be used and in some cases added additional locations needed to be inspected based on the nature of the damage mechanisms.
Recommendations included the use of Eddy Current Testing (ECT) and Phased Array (PAUT) Corrosion Mapping; RT was recommended on specific elbows and GWUT was recommended on the long straight piping runs. Process points that add risk were examined such as injection points and dead-legs and these observations were made part of the inspection plan.
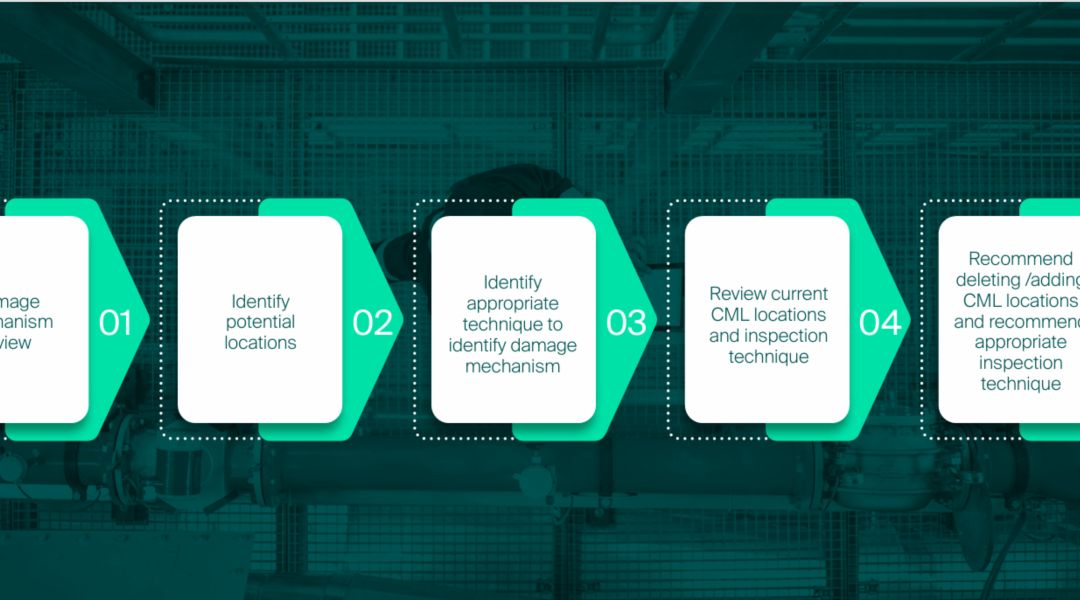
Figure 1: Non-Intrusive Inspection CML Review Workflow
Powerful results
We followed the recommended workflow to efficiently and cost-effectively develop the implemented guidance strategy (see figure 1 above).
Overall, we optimised the following CML locations:
6%
Reduced the number of RT locations by 6% - from 543 to 509 locations.
84%
Reduced the number of GWUT locations by 84% - from 132 to 21 location.
73
Added 73 previously unidentified locations to monitor for localised/pitting corrosion.
Other key benefits included:
- 27% reduction in inspection cost
- Significant time and cost savings by reducing unnecessary removal and re-installation of insulation (including cost of scaffolding and other mechanical related cost)
- Reduction in T/A resource downtime by reducing RTs and relating in the reduction of closed areas during x-raying
- Optimisation of resources and focus on higher-risk locations
- Reduced field activities to reduce risk exposure to field personnel
Overall these benefits resulted in shorter T/A time and cost.