Client
Due to commercial interests the client has requested to remain anonymous.
Asset
Gas processing plant
Result
Achieved up to 30% cost saving for inspection and maintenance of assets, between 80 to 95% reduction in failure risks, up to a 20% increase in equipment uptime and 50-90% reduction in inspection points.
Client challenge
Our client, owns a number of gas gathering, processing and transmission assets that services production. Vysus Group was commissioned to develop and implement a PSM MI (Process Safety Management Mechanical Integrity) programme for their a gas facility in the United States.
Operators are often faced with the challenge of optimising annual inspection and maintenance tasks, while maintaining safety and preventing the loss of containment. Poor execution of an integrated solution and lack of adaptation of advanced integrity technologies, can result in an increase in inspection and related maintenance costs.
How we helped
During a 4 month period, we implemented the PSM MI program using Lloyd’s Register’s (LR) AllAssetsTM Integrity Management Software for all Fixed Equipment, Piping Circuits, and PSVs for their facility.
An initial MI implementation was conducted on a ‘pilot’ unit as this helped define the workflow, identify potential issues, and finalise client specific project deliverables. Following the pilot implementation, the remainder of the program was carried out by applying our standard workflow process for implementing software enabled MI programs for our client’s facility. For typical implementations, the starting point is collecting all integrity related data and conducting a gap analysis. During the data collection phase, it is essential that the current availability of inspection isometrics/drawings is confirmed and quality established, as it is critical that these are available to clearly identify PSM MI test point locations to ensure reliability and repeatability of onsite inspections. However, for most implementations only partial drawings are available or original design/construction 3D models and/or fabrication isometrics. Availability of these can minimise onsite drafting requirements and speed up this phase of the MI implementation, however these should always be verified via onsite walkdowns and drawing updates.
With data collected, a corrosion study was executed and validated to identify key damage mechanisms and susceptibilities that pose threats to the assets - primary drivers for an effective PSM MI program. Data validation was performed after successful load into the database to ensure the dataset was accurate and provided the most effective MI program. Upon successful QA/QC of the data within the new database, criticality was assessed, and all associated inspection mitigation plans generated and implemented to help optimise inspections and build a sustainable integrity system.
A high-level overview of the implementation process is shown in Figure 1, with stages considered in scope shown in green, optional in yellow and out of scope in red.
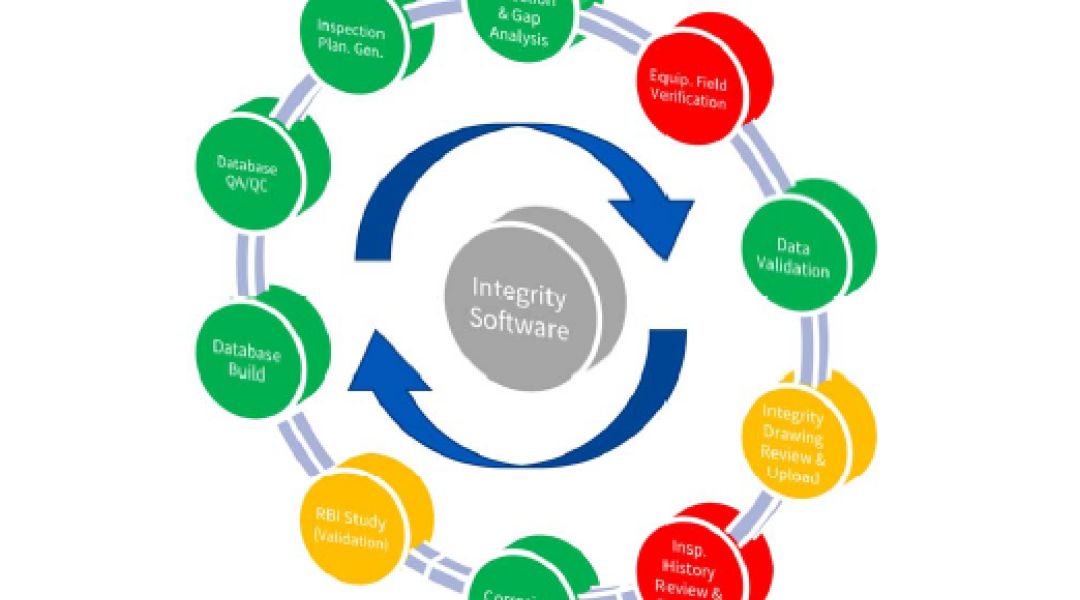
By working with Vysus Group, our client was able to modernise their MI program, capitalise on substantial OPEX savings and further enhance operational efficiencies through:
- Improvement of workflow process: centralisation of managerial decision making and integrated solution set.
- Management of personnel turnover: Implementation of competency assurance and knowledge management.
- Data Integration: Modernisation of data driven and real-time performance technologies.
An area of increased importance was the modernisation of current inspection and maintenance techniques and workflow processes, such as implementing software solutions that enable engineering-based decisions to optimise scopes. Modernisation of these techniques and concepts alone are not enough to effectively provide insight and visibility to emerging trends.
We used our Asset Performance and Risk Management system to help make better decisions faster which resulted in reduced unscheduled downtime, increased production levels and an understanding on the business risk exposure. When data is used effectively and managed wisely, it can enable organisations to achieve optimal operating costs, production rates, and safety performance in areas such as:
Time to value:
- Proven approach with preconfigured models, although customers can develop their own.
Focus limited resources on the most important items
- Predictive models
- Optimal life performance of the asset
Integrated processes that generate maximum ROI:
- Leverage existing EAM investments
- Reduce cost of ownership
Powerful results
On completion of the MI implementation programme, our client was able to effectively manage the cost relating to, integrity, risk, performance and reliability of equipment and assets. The program was able to determine the probability and consequences of equipment failure and safely extend the life of the assets to help achieve up to 30% cost saving for inspection and maintenance of assets, between 80 to 95% reduction in failure risks, up to a 20% increase in equipment uptime and 50-90% reduction in inspection points.