We asked a simple question: What would help you ensure the successful development and delivery of a supply chain for US offshore wind?
The US has a huge offshore wind energy resource and the industry is in ascendency. Today, there are development activities at different stages across 15 active lease areas. Tomorrow, the opportunities are even greater if equipment and components can be made in America. The American Wind Energy Association (AWEA) estimates a potential power of 2,000 gigawatts – almost double the nation’s current electricity use. While the next commercial-scale offshore farms in US waters will most likely rely on established European manufacturers, this is not seen as a long-term solution. The industry has widely recognised that evolving its own domestic supply chain is key to delivering projects cost-effectively.
At IPF19 in New York, the leading technical conference for US offshore wind, we held our own Twitter poll. We wanted to get a high-level industry view of the key challenges ahead. We asked a simple question: What would help you ensure the successful development and delivery of a supply chain for US offshore wind? We then presented several factors that could be instrumental in unlocking the potential. With the votes collated, we explore what the findings mean.
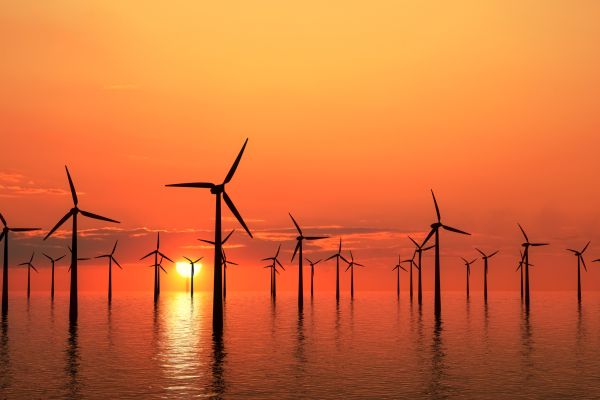
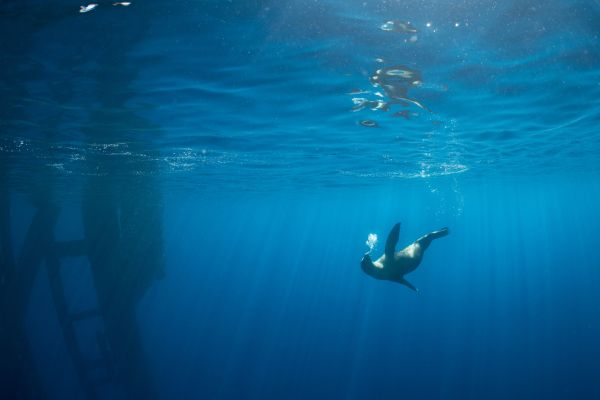
1. Visibility of projects
33% of votes
In any emerging market without a dedicated supply chain, domestic manufacturers wishing to service the sector must be confident in the pipeline of new projects. Take for example ‘Tier 1’ suppliers: manufacturers and installers of foundations and wind turbine generators (WTGs). These companies will need to invest significantly in manufacturing bases and facilities, alongside developing a skilled workforce. None of this is cheap and simply won’t happen without there being a clear, continuous demand for components. ‘Scale and volume’ is the industry’s mantra.
For other tier suppliers new to the market, project visibility will mean other important things. Until expertise is built up, niche companies will lack a full understanding of what their wind farm developer clients require and to what timescales. They will need the right support if they are to enter the procurement process successfully and deliver on time, to budget. The question is who will help with that?
State agencies could step in to play match-maker. Connecting developers and potential suppliers in ‘share fairs’ would help to quickly bolster knowledge on how all parts of the value chain fit together. This would bring an ever-popular benefit: local economic growth. There is a hurdle to overcome, however. In the US, government procurement is predominantly undertaken on an extremely competitive basis. Cheaper wins contracts. The outcome is that developers can be reluctant to disclose their plans in detail. Encouraging a more open culture is crucial.
State agencies could also help with the right skills’ development. Some are already thinking about this. At vocational colleges across New York State, Massachusetts and Rhode Island, offshore wind training curriculums and facilities are being established. This is a positive sign, as long as timescales can align with an evolving industry’s needs.
The American Wind Energy Association (AWEA) estimates a potential power of 2,000 gigawatts – almost double the nation’s current electricity use.
2. Network of ports
30% of votes
Europe was fortunate when it came to a supply-chain infrastructure for offshore wind power. As the industry developed within the same footprint as the oil and gas business – predominately in the North and Baltic Seas – there were numerous heavy industrial port facilities along the coastline nearby to development areas. These facilities, spanning many hundreds of acres, lent themselves readily to supplying large-scale wind turbine components.
The US port situation is not so serendipitous for an offshore wind industry that will emerge from northeast coastal waters that is far from the mega-sized industrial port facilities serving the oil and gas sector in the Gulf of Mexico. In comparison, waterfront industrial facilities in the northeast are smaller, stretching to a couple of dozen to a few hundred acres in size at most. They also tend to be either distressed brownfield or greenfield sites. These factors present major regulatory and environmental challenges for offshore wind development.
Most experts agree on the best solution: a network of smaller port facilities to support the buildout of wind farms. Such facilities will need to be interconnected by another new sector: a logistics industry to heavy lift turbine components. Clearly, there are risks here that European developers avoided. These issues must be addressed swiftly if the domestic offshore wind industry is to continue on its current trajectory.
3. Port funding
19% of votes
Europe and the US also differ when it comes to funding port infrastructure for offshore wind use.
European ports benefitted from public funds and public-private partnerships by and large. These initiatives brought the investments necessary to convert existing facilities. In the US, the source of the large sums required to develop a network of interconnected ports has yet to be identified.
While individual states are beginning to pledge funds, a coordinated investment approach is lacking. The good news is that significant US equity is interested in developing port infrastructure. Investors are simply waiting for the right conditions to happen before acting. These conditions should start to fall into place as the pipeline of offshore wind projects grows in the US.
While individual states are beginning to pledge funds, a coordinated investment approach is lacking.
4. Development incentives
18% of votes
Incentives to encourage wind farm development are also on the industry’s mind. This is for good reason. Such incentives have been a key component in making offshore wind a US reality to date. They include Investment Tax Credits (ITCs) to develop renewable energy. However, ITCs are being phased out in the coming years, with the repercussions yet to be fully grasped. Developing new technology and more efficient construction and installation processes will help to address this challenge, lowering overall development costs.
Related Services