Measuring wall thickness is critical for several industries and many of our clients. Conventional methods of doing this, however, are costly, timely, restrictive and error prone. We partnered with Inductosense to offer a better way forward, saving on recurring costs.
Wall thickness measurements give invaluable insight into the internal corrosion and erosion of piping, pressure vessels and structural steels. Thickness data enables offshore and onshore operators to assess the condition of their assets. Monitoring the rate of thickness-loss supports predictive maintenance, which helps optimise asset integrity operations and reduce downtime.
The two most common ways of acquiring thickness data are through manual ultrasonic testing (manual UT) or by using a permanently installed monitoring system. Each method presents its own commercial challenges.
The challenges with conventional methods
Manual UT demands skilled personnel, which can be a high recurring cost. Acquiring thickness readings can take time and there is always the risk of human error, leading to inaccurate data and flawed decision making.
Using a conventional permanently installed monitoring system is also problematic. For starters, the technology has a high capital cost, and a power-and-network setup is required, which can be a logistical headache. The solution can also be frustratingly limited when needing to measure thickness of insulated or coated assets.
The reliable, repeatable, cost-saving solution
Vysus Group is continually looking for ways to further support clients in optimising the costs associated with monitoring inspection points. We have partnered with UK-based ultrasonic solutions provider, Inductosense, to promote the company’s innovative WAND system, both to clients directly through demonstrations and our wider consulting services, and collaboratively at industry conferences.
We were immediately struck with how well the technology works in solving today’s challenges. It provides a new way of monitoring thickness safely, reliably and efficiently – free of human error and at scale – even for remote assets and locations that are difficult to access. Thickness data can be collected easily and frequently from locations at height, or that are obstructed, without scaffolding, rope access or similar requirements. Underground installations can be monitored from an above-ground terminal without requiring direct access to the equipment, as well as under insulation without the need for inspection ports and coatings. WAND sensors can be embedded underneath insulation, coatings and composite wrap repairs, and wirelessly activated through the material using inductive coupling technology.
Quick and easy thickness readings
The WAND system is a three-part solution that generates precise, repeatable wall thickness readings for accurate internal corrosion monitoring and trending. It can be installed quickly, and data can be acquired straight away with no extra IT infrastructure needed. As shown in the supporting illustration, the system comprises:
permanently installed, battery-free, passive ultrasonic sensors, which are placed or embedded at corrosion monitoring locations in conditions of -45C up to 130C; the sensor provides an accuracy of 0.05mm and is able to trend and detect corrosion of 0.02mm
the option of handheld or remote data collector devices to wirelessly provide power to collect and upload thickness data, supported by several accessories depending on the application requirements
cloud software to configure the devices, manage and analyse data anywhere, and inform decisions. On a browser or using a universal app, asset operators can view thickness data trend graphs, analyse A-scans, calculate internal corrosion and/or erosion rates, export raw data and images, and generate reports
From the design stage to running ageing assets, Vysus Group helps operators to safely deliver improved performance, focusing on inspection and maintenance where it counts.
The benefits of using new technology
The WAND is designed so that anyone can take an ultrasonic measurement in the field, with the simple press of a button. The system has a number of advantages over alternative thickness monitoring methods, including the following core benefits.
Waving a WAND around in the field
The WAND system has already led to significant cost savings for those adopting the technology, both onshore and offshore, including several global operators.
For example, refinery and chemical plant operators have been able to monitor thickness without insulation removal, scaffolding or ropes, reducing time and labour costs associated with thickness data collection and reporting. An offshore well operator was able to use personnel already on site to carry out thickness monitoring. Previously, specialists had to be flown in. A pipeline operator was able to carry out thickness monitoring of unpiggable locations for a fraction of the labour cost. Back on shore, a well operator who replaced its sensors with WAND ones reported a ten times lower CAPEX spend, while an onshore gas plant operator saved on the expensive business of cleaning and surface preparation demanded by manual UT.
An additional advantage is that the price of WAND sensors drops significantly as the volume increases. In our experience of supporting clients, this can make the cost per monitoring location far lower than the alternatives out there.
Another technology partnership from Vysus Group
From the design stage to running ageing assets, Vysus Group helps operators to safely deliver improved performance, focusing on inspection and maintenance where it counts.
Clients benefit from our in-depth understanding of asset management, encompassing equipment, people, processes and data, to safeguard asset integrity effectively. We help reduce failure risk by up to 95% and inspection points by 50-90%, and have partnered with Inductosense to further support clients in optimising their monitoring activities. Inductosense is based in Bristol, UK. The dynamic team of industry specialists designs, develops and manufactures its ultrasonic solutions in house.
In partnership with
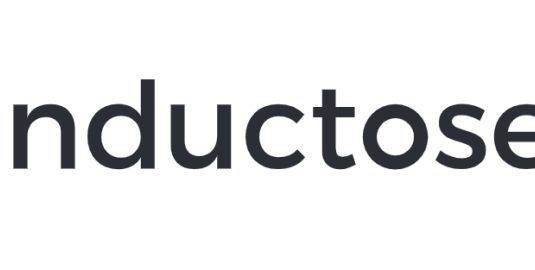