Article | Gordon Ellis | 30.03.2022
Developing a maintenance strategy that fits
In February 2020 I travelled to Southern Italy to conduct a kick off maintenance improvement project at a chemical plant belonging to one of our international clients. Our client has acquired a number of plants around the globe and has a well-defined and well-structured improvement methodology as illustrated in the diagram below.
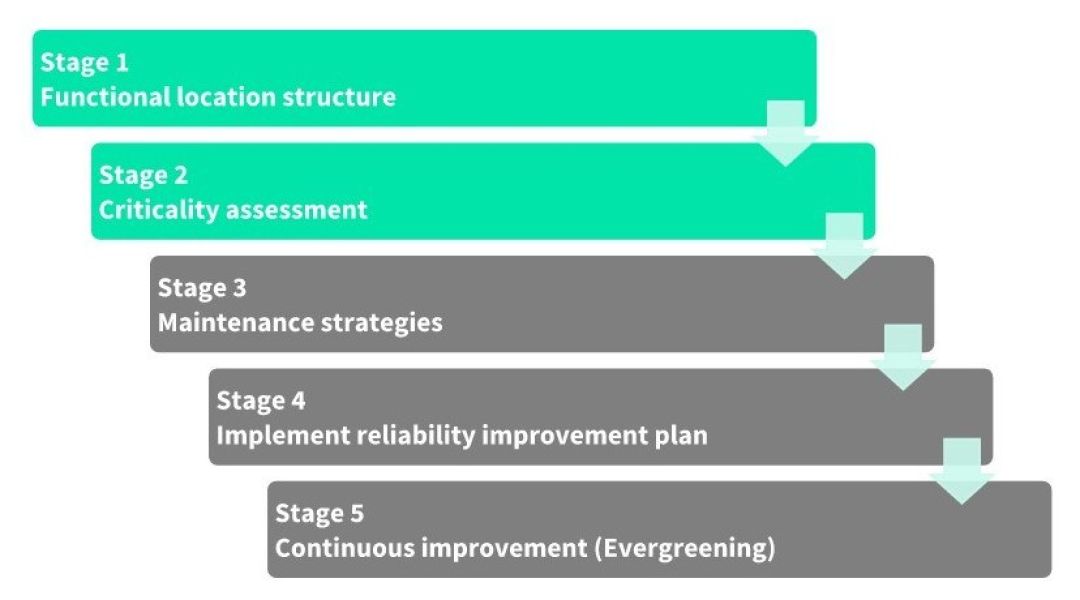
This kick-off meeting, was for Stage 1 getting the foundations correct by rebuilding the functional locations within SAP to the client's corporate standard. It was meant to be a combination of remote activities such as reviewing the functional locations and equipment against the P&IDs and SLDs to restructure them in accordance with the corporate standard. The remote work was to be supported by 2 onsite workshops the first to develop a set of site specific rules covering for example how we would structure instrument lops and also how equipment would be translated over and existing tag number retained etcetera. The second was to be a review workshop of the outcome.
Of course, little did I know as I travelled back to the UK after the meeting just how much of an impact the global pandemic was about to have around the world. We quickly had to find a way of working effectively in an international multilingual manner and expanded an existing query register to allow us to set the reviews and conduct workshop sessions remotely.
At the end of stage 1, we delivered an updated functional location structure and equipment loading templates for upload in to the client's corporate SAP system. Having the functional locations align with their corporate standards ensures consistency and allows them to maximise efficiency across their global operations and be consistent in their KPI measurements.
Due to other priorities at the plant and the impact of the ongoing pandemic we had a pause on completion of stage 1 before commencing stage 2 criticality assessment. The client considers criticality across 5 risk categories The criticality is set on a mixture of documentation such as HAZOP and cause and effects along with workshops to capture the detailed site knowledge. Where we had done them in the past, following the upfront preparation of reviewing the Cause and effects etc. We would have attended the site for two intensive workshops each over several days. We knew of course that this would not work online so in consultation with the plant arranged several half-day workshops spaced a couple of weeks apart. This, of course, meant then the entire program became extended but on the plus side, it helped to minimise the interruption to the site of taking some of their most knowledgeable people out for a workshop. We found the key was for us all to work collaboratively and remain flexible. We are now at the point where we are arranging the final review workshop with corporate to complete some final quality checks and close out a couple of technical queries. This will allow us to deliver the load sheet with the criticalities set and the P&IDs marked up to show critical equipment. The client uses criticality to prioritise work, ensure spares are available for critical equipment and understand the risks associated with the failure of equipment.
During the review workshop, we will also discuss Stage 3 developing and implementing maintenance Strategies. We will start by reviewing what the client has available already both at the plant in Italy but also some of the sister plants in other locations that are slightly further ahead on this journey. This stage will also include a review of the plant CMMS history data along with interviews with the plant operators and maintainers to see how effective maintenance has been in the past and identify any bad actors. We will also investigate the current spares strategy and how it is implemented on-site. One of the main outputs from this phase is the defined scope for phase 3.
In stage 4 we will go about applying the criticality based maintenance with the major output being a sustainable maintenance and inspection program. In Stage 5 Key Performance Indicator dashboards are set up to drive continuous improvement.