Amine systems are notorious for corrosion-related problems that are complex to solve and sometimes unobserved. Engineers have regularly been surprised to discover corrosion damage during a routine internal inspection, or even worse by a failure during operations. By way of illustration, an article in The Chemical Engineer examined 375 cases of amine system failure, each of which resulted in $250K to $250M of lost production[1].
One of the reasons for the high failure rate on amine systems is their complexity. Several driving factors contribute to corrosion problems, making it challenging to identify the root cause. Every amine system is unique due to the feedstock properties, design conditions and operating philosophy. However, amine corrosion issues can be solved with the right level of plant information and engineering experience.
How amine systems work
The Oil & Gas and Liquified Natural Gas (LNG) industries are traditional users of amine systems. Another significant amine user is for Carbon Capture and Storage (CCS) technology which can be associated with power generation or production of chemicals and renewable fuel sources such as hydrogen, biomethane, etc. These applications need to remove CO2 or H2S or both from their gas streams. The need for purification may be driven by emissions limits for environmental compliance or protection of downstream processing units. LNG transfers also have specification limits for the CO2 and H2S content to prevent corrosion in pipelines and to ensure a minimum heating value of the product. All amine systems have a similar process design.
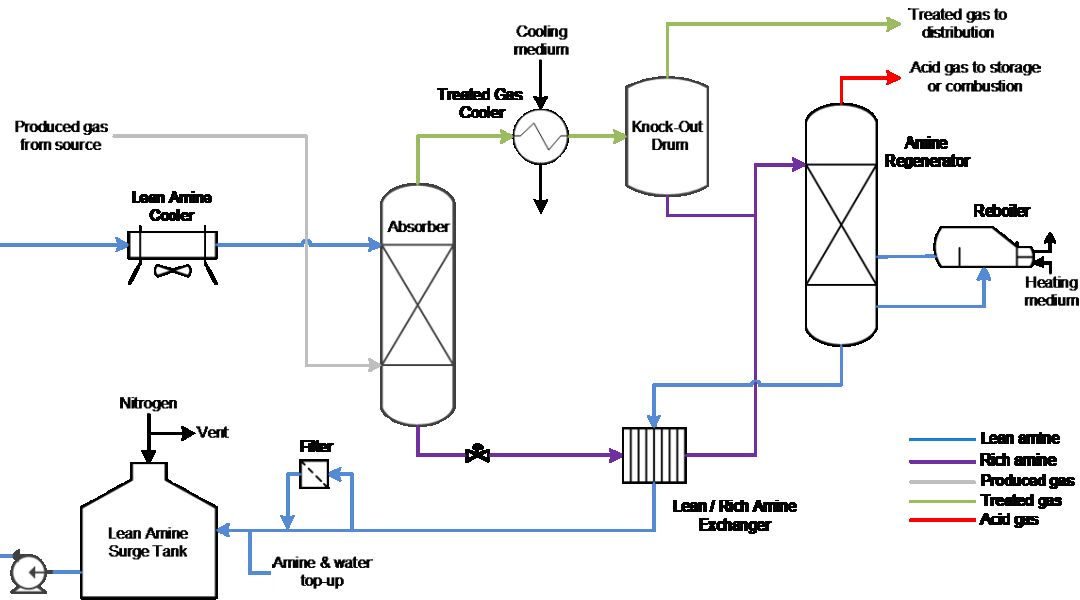
Amine systems have an absorber for removing CO2 and H2S from the sour gas stream and a regenerator for cleaning the amine. As such, the amine operates in a near closed loop where it is continuously recycled and reused. Top-up amine and make-up water compensate for losses from the top of the regenerator.
Recycled amine enters the top of the absorber. It is known as lean amine because it is free of CO2 and H2S. At the same time, process gas is rising from the inlet at the bottom of the tower. Packing or trays in the absorber ensure maximum contact between the gas and the amine for absorption of CO2 and H2S. The amine leaving the bottom of the tower is loaded with CO2 and H2S and is known as rich amine. This rich amine passes through a regenerator where contaminants are stripped out of the chemical to make it lean amine again. Clean process gas exits the overheads of the absorber for further processing or transfer, whilst acid gas (rich in CO2 & H2S) from the overheads of the regenerator is either combusted on-site or transported off-site to underground storage.
Common causes of failure in amine systems
As has been already noted, the complexity of amine systems makes them susceptible to corrosion in several different ways. Some of the most common failure causes are as follows:
- Localized corrosion in rich amine lines due to vapor flashing. This happens when rich amine releases CO2 or H2S before reaching the regenerator, where this release is designed to occur.
- Stress corrosion cracking in carbon steel piping where there has been no post weld heat treatment (PWHT).
- Degradation of the amine. Virgin amine contains less than 1% of heat-stable salts, but these build up over time due to continuous recycling. Levels of 2 to 3% and higher can lead to corrosion on the lean amine circuit. Other causes of amine degradation are high temperatures and contaminant ingress.
- High fluid velocity or turbulence causes erosion-corrosion of piping and equipment. This process condition can occur after the feed line control valve, or in reboiler return lines.
Case study
An Exploration and Production company recently discovered corrosion problems on an amine system, which they were not expecting. A routine internal inspection of the amine absorber revealed localized corrosion, especially in the region just above the liquid tide line as shown in Figures 1 and 2. Vysus Group participated in the investigation to identify the causes and make recommendations about future use until the operating company could implement permanent repairs.
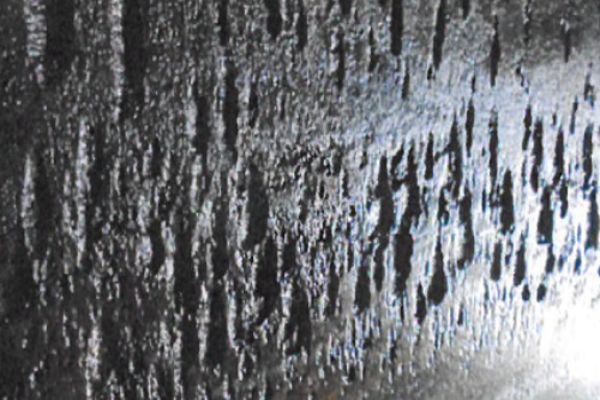
Figure 1 - Heavy pitting around circumference of the vessel at the tide line
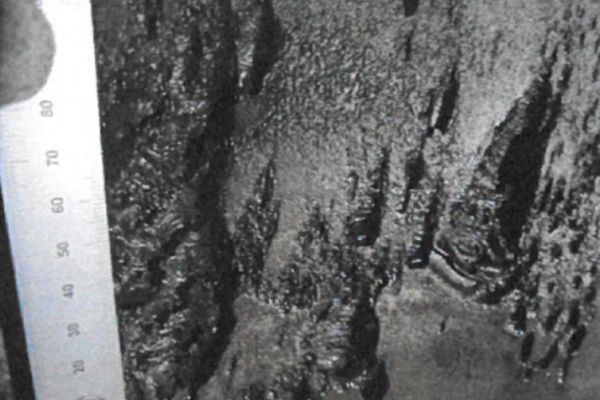
Figure 2 - Close up of pitting corrosion
The project team found a significant contributing factor to be a change in feedstock since the last inspection. A new feed stream with a much higher CO2 content was introduced causing the combined feedstock to exceed the amine system design conditions at the desired gas throughput. As a result, the amine was being loaded with very high levels of acid gas and the exothermic process of absorption was leading to excessive temperatures in the absorber. These combined conditions led to acid gas flashing above the liquid level and acidification of the amine solution resulting in corrosion pitting at high rates.
Vysus Group, together with the client team, produced a detailed report describing the corrosion mechanisms and corrective actions. Ultimately, it was necessary to upgrade the material design of the absorber with a corrosion-resistant weld overlay. However, the facility needed to continue operation for at least another year in order to arrange a planned shutdown for such a major modification.
Recommendations for continued operation involved limiting the new feedstock within the total amine system supply to reduce amine loading and internal temperatures. Also, a new temperature transmitter was installed on the absorber to give better insight into its temperature profile. Regular iron count monitoring downstream of the absorber provided a means to identify signs of a corrosive process regime. Finally, updated fluid monitoring programs, for oxygen contamination and heat stable salt accumulation helped to keep constant vigilance on the amine quality and process dynamics.
How Vysus Group approaches amine system corrosion problems
Amine systems are notoriously prone to failure and are complex to troubleshoot when they exhibit corrosion issues. However, Vysus Group has worldwide experience in Amine systems in a diverse range of applications. Drawing on this global experience base, Vysus Group has the technical expertise to help solve amine system corrosion. We work together with our clients to investigate, analyse and make recommendations using a proven engineering process:
- Develop an understanding of root causes by collection and analysis of plant information, design conditions and process changes
- Diagnose failure mechanisms and contributing factors
- Make recommendations like material upgrades, fluid monitoring, or setting new process conditions
Contact Vysus Group for help to solve your amine system corrosion problems.